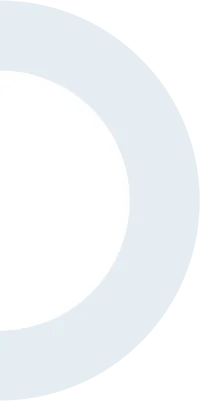
Cylinder Liners & Sleeves are the most important functional part of an engine that are integrated with the engine block and form the combustion chamber. Both of these products have different applications as per the engine specifications.
The cylinder liner, serving as the inner wall of a cylinder, forms a sliding surface for the piston rings while retaining the lubricant within. The most important function of a cylinder liner is it’s excellent characteristic, a sliding surface and these four necessary points.
High anti-galling
properties
Less wear on the
cylinder liner itself
Less wear on the
partner piston ring
Less consumption
of lubricant
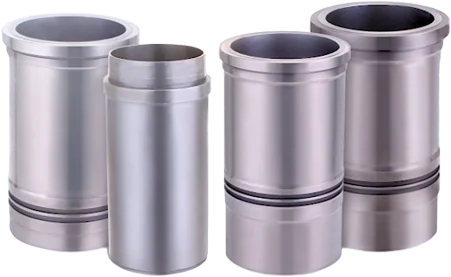
Cylinder Liners
Liners are centrifugals casted with thick wall thickness. They do not directly come in contact with engine block and are a part of the water jacket. They are used typically in heavy duty engines.
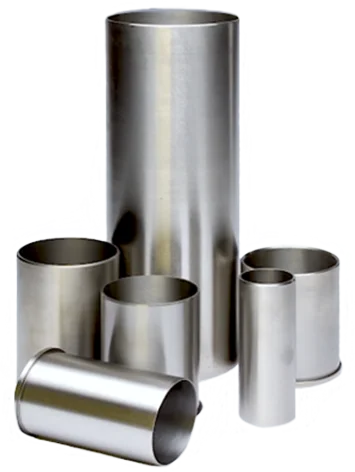
Cylinder Sleeves
Sleeves are identified with ones having very thin wall thickness. They are directly in contact with engine block and not the coolant. They can achieve downsizing and weight saving of engines as they can make bore clearance smaller by their design. These can also be manufactured with phosphate coating to improve abrasion resistance.
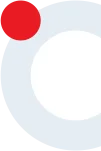
Cylinder Liner & Sleeve Sizes
Inner Diameter | 50 mm minimum till upto client’s requirement |
Outer Diameter | 70 mm minimum till upto the client’s requirement. |
Length | Upto 500 mm |
Weight | Upto 200 kg |
Grade | As per client requirement |
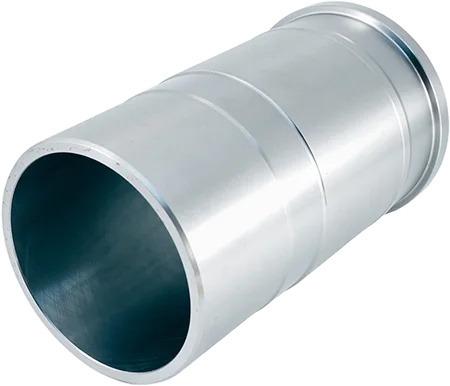
Quality Assurance Process
A cylinder wall in an engine is under high temperature and high pressure, with the piston and piston rings sliding at high speeds. In particular, since longer service life is required of engines for trucks and buses, cast iron cylinders that have excellent wear-resistant properties are used.
Also, with the recent trend of lighter engines, materials for engine blocks have been shifting from cast iron to aluminum alloys. However, as the sliding surface for the inner cylinder, the direct sliding motion of aluminum alloys has drawbacks in deformation during operation and wear-resistance. For that reason, cast iron cylinder liners are used in most cases.
- All our process is done in house. Our facility is equipped with ultra modern foundry, machine shop and laboratory. The molten material is thoroughly checked under spectro and microscope for its grains and chemical composition before casting.
- Machine shop is equipped with CNC’s, centerless grinding machines and honing machines.
- Required surface finish in bore are achieved by honing machines. They are also tested with sophisticated surface tester. Also, cross hatch angles are achieved in this process.
- We also do Millipore testing after ultrasonic cleaning to make sure highest cleanliness of our product.
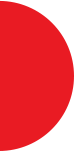